STABILIZATION OF SUBMERGED AIRCRAFT
ENGINES
(translated by the CCI Ottawa)
Abstract
In June 1944, allied forces shot down a Luftwaffe Focke-Wulf 190 fighter
over France.
The aircraft crashed in Le Loiret River and remained there for 45 years,
until it was
recovered in August 1990 by the Club Subaquatique d'Orléans. It
was then deposited
in the Caen Memorial, Museum for Peace. This report presents a typical
case of
stabilization of an aircraft engine following a rolonged period underwater.
Here we
follow the story of the conservation of a BMW 801 D2 twin row radial engine
as carried
out by the Valectra Laboratory, which developed a satisfactory treatment
protocol.
A Focke-Wulf 190
Introduction
Objects made of aluminum alloys are often found in the reserve collections
of technical museums; although these are relatively new metals (their
industrial production dates from the late nineteenth century), they are
an intrinsic part of the history of the technologies and industries that
emerged with the twentieth century, such as aeronautics.
They are of particular interest to the public because they are closer
to us and are still being used and developed today. Such objects include
a number of aeronautical artifacts recovered from rivers and oceans, most
of them dating from the last two world wars. The history of civil aviation
also includes some tragically well-known wrecks, including those of Nungesser
and Coli [1], Mermoz and Earhart [2]. A number of dedicated organizations
are interested in this little-known heritage: TIGHAR (The International
Group for Historic Aircraft Recovery, 2812 Fawkes Drive, Wilmington, DE
19808, USA) not only carries out regular exploration campaigns but also
supports research programs on the conservation of light alloys, such as
those conducted by Hallam [3] at the Australian War Memorial (AWM) in
Canberra.
When a submerged artifact of this kind is located, there is an enormous
desire to recover it, but a number of unfortunate recent experiences (the
Arado 96 [4] and the Dornier 24s [5] from the lakes of Landes) have demonstrated
the extreme instability of this type of object when exposed to the atmosphere;
the corrosion already present is rapidly exacerbated, leading in more
or less short time to the destruction of the object. The first treatments
on submerged aeronautical artifacts were performed by MacLeod [6], who
proposed immersing an aluminum-copper alloy seaplane float in an ammonia
solution. Since 1987, numerous additional studies have been performed
in France, particularly by the Valectra Laboratory of Electricité
de France, and have led to the development of a less time-consuming method
of treatment using electrolysis [7-9], which can be used for associated
composite systems, since aluminum alloys are rarely found in isolation
[10].
They are, in fact, often associated with iron alloys (engines and fuselages),
with copper alloys (aircraft equipment), less commonly with magnesium
alloys (which have almost totally disappeared) and, finally, with non-metallic
materials such as wood, leather, rubbers or plastics.
Following a brief summary of the corrosion problems encountered on submerged
aeronautic artifacts and the state of knowledge in the area of treatment,
we will look at the typical case of the BMW 801 D2 twin row radial engine
from the Focke-Wulf 190 that was shot down in June 1944 by Allied forces
and crashed in Le Loiret River, where it remained for 45 years until it
was recovered in August 1990 by the Club Subaquatique dOrléans
(France). Before it was deposited in the Caen Memorial, Museum for Peace,
the Valectra Laboratory stabilized it, developing a satisfactory treatment
protocol in the process. The work was carried out with the assistance
of two specialists from the AWM [11].
State of knowledge
on the treatment of corroded aluminum alloys
-Top
While some aluminum alloys are known for
their high resistance to saline atmospheres, those that are found on submerged
aeronautical wrecks show significant corrosion as a result not only of
the aggressive nature of the surrounding environment but also of the composition
of the alloys. Despite a number of instructive counter-examples, such
as the Loch Ness Wellington [12] found partially buried in the bottom
of the lake at a depth of 80 m, the immersion medium is rarely harmless
to these materials; the chloride ions present, even in small quantities,
cause extensive damage, which is localized at first (pitting and intergranular
corrosion) but eventually becomes generalized. In addition, the noble
metals (steel and copper alloys) in contact with them create local galvanic
cells which can lead to the virtually complete disappearance of the aluminum
alloy parts on certain artifacts.
With the exception of seaplanes, which are specially protected, most aircraft
are not made to withstand the damage caused by prolonged immersion in
a marine environment. The alloys used in the first half of the twentieth
century invariably contained copper, which considerably enhances their
mechanical resistance properties but increases their sensitivity to the
different forms of corrosion. After long immersion, a double layer of
corrosion is formed, but it offers very little protection: the oxidized
layer adhering to the metal surface is thin (0.2µm), while the layer
covering it is pulverulent and contains all the polluting species, both
metallic and non-metallic. Other common alloys, such as those containing
manganese or a magnesium-silicon combination, are covered by hydrated
white pustules over hemispheric pits. All these states are unstable in
the atmosphere, because of the presence of chloride ions at the bottom
of the active zones [7].
To stabilize these materials, we have for a long time opted for an electrolytic
dechlorination of the alloys by cathodic polarization, which can be performed
only within a very limited range of potentials and pH values to avoid
the risk of pitting corrosion due to the chloride ions already extracted
and present in solution, and of cathodic corrosion caused by the deterioration
of the insulating properties of the surface oxide film as a result of
cathodic polarization. In practice, the chloride ions are eliminated at
an imposed potential, in a slightly acid, buffered (pH = 5.4) and stirred
sodium citrate solution [7-9]. Because of the heavy pollution of the surface
corrosion products by iron (due to the corrosion of steel objects in the
vicinity) and possibly by copper (in the case of aluminum-copper alloys),
these unstable compounds are dissolved before hand without polarization
in a similar solution which has useful chelating properties. This approach
avoids the risks of metal deposition in the case of direct polarization
and, in addition, limits the thickness of the corrosion layer through
which the chloride ions must diffuse. On completion of these steps, the
object is rinsed in demineralized water or in tap water (under cathodic
protection to avoid any fixation of additional chloride ions) and then
dried.
While this treatment is satisfactory for objects containing only a single
alloy, it is not appropriate when an alloy is associated with noble metals
such as steel or copper alloys (bronzes, brasses and coppers). In this
case, contact between the different metals has caused galvanic phenomena
during prolonged submersion, resulting in accelerated corrosion of the
light alloy to the benefit of the noble materials, which are well preserved
but covered with concretions of varying thickness contaminated with chloride
ions that must be removed during treatment. Those distributed on the metal
surfaces can be eliminated by immersion in the buffered sodium citrate
chelating solution. The mechanical action of the hydrogen bubbles formed
at the interface between the metal surface and the concretions, provoked
by cathodic polarization of the ferrous parts during a second step (a
good metal core is required for this), permits the removal of the harder
concretions. This cathodic treatment for cleaning iron alloys is performed
in a basic solution to prevent corrosion in the event of improper polarization
(the alloys would then become covered by a passivating oxide film). Caustic
soda and potassium solutions are too corrosive on aluminum alloys; another
electrolyte is therefore proposed for composite objects.
Weight loss (%)
Silicate concentration (M)
-Top
Figure 1. Weight loss measurements for an aluminum-copper
alloy versus the silicate ion concentration, after three weeks of immersion.
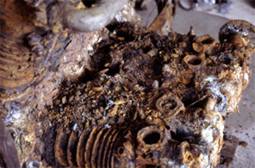
Figure 2. View of the FW 190 BMW 801 D2 engine from Le Loiret River
before treatment.
During similar treatments performed on a Pratt & Whitney engine at
the AWM, we found that sodium metasilicate Na2SiO3 was suitable because
of its corrosion-inhibiting properties on aluminum alloys [10]; however,
it was determined that, beyond a concentration of 0.08 M, significant
corrosion occurred, with the formation of fibrous white aluminum silicate
compounds. We therefore repeated these studies, establishing, in accordance
with ANSI (American National Standards Institute) standard G-172, mass
loss curves for aluminum-copper alloys (Figure 1) and aluminum-manganese
or aluminum-magnesium-silicon alloys (materials commonly found in aeronautical
wrecks) that are non-corroded and immersed in metasilicate solutions at
various concentrations.
We found that the usable range of inhibitor concentrations (no evident
corrosion) is broader for alloys without copper than for aluminum-copper
alloys.
0.05
M < Cinhibitor
for Al-Mn < 0.45 M approximately;
0.05 M < Cinhibitor for Al-Mg-Si < 0.3 M approximately
and
0.05 M < Cinhibitor for
Al-Cu < 0.25 M.
These tests were then repeated using identical materials that had been
corroded as a result of immersion for 40 years in fresh water (Lake Biscarrosse,
Landes). This time, we found that the usable concentration ranges were
significantly lower. For instance, for aluminum-copper alloys, which are
the most sensitive to any form of corrosion, the safe range is below 0.05
M; for clean materials, in contrast, only surface tarnishing occurs at
this level. These low inhibitor concentrations are explained by the fact
that it is difficult to form a protective layer when the material is already
covered by corrosion products. If the concentration increases, the inhibitor
combines with these products and protection becomes impossible, as was
observed indeed on the AWMs Pratt & Whitney engine. In order
to retain a conducting solution, a concentration of 0.04 M was finally
selected, with a pH of 12.4.
Table I. Composition
of the aluminum alloys found on the BMW 801 D2 engine
Description |
Principal
elements |
Secondary
elements |
Designation |
|
|
|
|
Piston
|
Si
|
|
Type
4XXX alloy |
Cylinder
head |
Mg-Si
|
|
Type
6XXX alloy |
Cylinder
cap |
Mg-Si |
|
Type
6XXX alloy |
Intake
pipe |
Si |
|
Type 1XXX alloy |
Connections |
Si
|
Cr
|
Type
4XXX alloy
chrome-plated surface |
Registration
plate |
Si
|
|
Type
1XXX |
The procedure selected
for the treatment of aluminum alloy/iron alloy composites is summarized
below:
_ pretreatment of the entire object by immersion in a chelating buffered
sodium citrate solution (pH = 5.4);
_ removal of concretion (if necessary) from the ferrous parts by cathodic
polarization in a stirred sodium metasilicate solution (0.04 M);
_ dechlorination of all metal parts of the object by cathodic polarization
in a stirred and buffered sodium citrate solution (pH = 5.4);
_ final rinse of all metal parts of the object in tap water under cathodic
protection to eliminate citrate species.
Following these operations, the item must be completely dried before any
protection is applied.
Description of the BMW 801 D2
engine and diagnosis before treatment
-Top
Figure 3. Radiographic image of a cylinder head from the BMW 801 D2
engine.
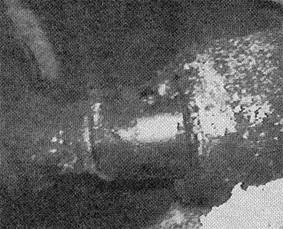
Figure 4. Fibroscopic image of the interior of an intake pipe, showing
one of the valves.
This engine came from the most advanced German fighter aircraft of the
Second World War, the Focke-Wulf 190. The original design was based on
a Pratt & Whitney licence and consists of 14 cylinders in a twin row
with direct injection (Figure 2). The lower part of the engine still reflects
the violence of the impact: six cylinders have been ripped off. In addition
to aluminum alloys (Table I) and iron alloys, it contains traces of magnesium
alloys as well as rubber and various polymers. The apparent good state
of preservation of the metal parts has been confirmed by radiographic
and fibroscopic imaging. X-rays taken of one of the cylinders (Figure
3) and of the propellor speed reduction unit, with the assistance of a
miniaturized linear accelerator called MINAC, show no cracks in the objects.
A fibroscopic probe, inserted into the cylinders and intake and exhaust
pipes, showed that the degree of corrosion inside the engine is very similar
to that found on the exterior pitting on the aluminum alloys and thin
concretions on the iron alloys (Figure 4).
Table 2.
Analysis of corrosion products present on certain metal surfaces of the
BMW 801 D2 engine
Description |
X-ray
diffraction |
X-ray
fluorescence
(principal elements |
Engine core |
CaCO3, calcite
FeCO3, siderite |
Ca, O |
Exhaust pipe |
CaCO3/FeCO3
FeOOH, goethite |
Ca, Fe, O |
Rear gear wheel,
engine |
Mg6FeCO3(OH)13×4H2O
brugnatellite
MgCO3×3H2O, nesquehonite |
Fe, Mg, O |
Piston |
CaCO3 Pb, 3PbO×H2O
PbCO3, cerusite |
Ca, O |
Analysis of the corrosion products present on the various materials (Table
2), obtained by X-ray diffraction and X-r
ay fluorescence, revealed the presence of calcite (CaCO3) and quartz (SiO2)
over the entire engine (derived from the environment in which it was submerged),
ferrous hydroxide and carbonate on the iron-based alloys, and extensive
white agglomerates of magnesium carbonate and hydroxide on the remaining
magnesium alloy parts. No aluminum-based compounds, however, were found.
It should be noted, finally, that the aluminum-silicon alloy pistons are
covered with lead oxide under the layer of calcium carbonate, probably
from the lead contained in the lubricating oil or fuel used. No chloride
compounds were identified, possibly because of the non-aggressive environment
(fresh water) in which the engine was submerged.
The aluminum alloys were not seriously corroded despite direct contact
with ferrous parts. The use in this engine of aluminum-magnesium-silicon
alloys, which are more resistant than aluminum-copper alloys, is of interest,
since it is rare to find them in such proportions on artifacts from the
Second World War.
Treatment of this engine thus amounted primarily to surface cleaning rather
than stabilization by the extraction of chloride ions. Nonetheless, we
applied the complete procedure for an iron alloy/aluminum alloy composite,
in order to test it under standardized conditions for the treatment of
a large object.
Description of the treatments
-Top
The metal surfaces were covered with weakly adherent agglomerates, mixtures
of corrosion products and debris from the environment in which the aircraft
was buried. Since these agglomerates are likely to produce rapid saturation
of the chelating sodium citrate solution used for the first phase of the
treatment, a preliminary mechanical cleaning was performed. To avoid direct
handling of the engine, a specially designed steel support was developed
to permit safe and easy movement. Since one third of the engines
cylinders were missing, the most complete (and therefore the heaviest)
part was tipped down. The system thus obtained was not only more stable
but also more compact (Figure 5).
Figure 5. Immersion of the engine in the tank for
dissolution of the corrosion products in a buffered
sodium citrate solution (pH = 5.4).
Dissolution
of surface corrosion products
-Top
The buffered sodium citrate solution is prepared in intermediate vats
because of the large quantities required: 42.5 kg of anhydrous citric
acid and 21.25 kg of caustic soda to 4.43 m3 of solution to produce a
pH of 5.4. Because of the solutions strong chelating capacity, the
steel tank required cathodic protection. Preliminary tests showed that
cathodic polarization of the steel at a potential of -1.2 V/SSE (SSE =
saturated mercury sulphate electrode) would prevent any corrosion (no
discolouration of the solution and no change in pH: high consumption of
Fe2+ ions would, in fact, result in saturation of the solution, which
would turn yellow as the pH increased). An Acore RGT 444 generator was
used; the necessary potential was obtained with a cell voltage of 2V and
a 5A current. Electrical contacts were provided by heavy cables fastened
to the walls of the tank, and to the expanded 304 stainless steel anode
cage placed inside it, by means of bolts, also made of stainless steel.
Any interference with the treatment due to the corrosion of the tank being
prevented, the engine was submerged (Figure 6) and positioned on the bottom
of the tank, insulated by a PVC (polyvinyl chloride) plate. The lifting
system was left in place so that the engine could be raised at any time.
The pH of the solution was monitored throughout this step (seven days).
Figure 6 shows its evolution: there is a progressive rise, probably due
to slight corrosion of the iron in the support and the iron alloy parts
of the motor (crankcase, gears and cylinders), followed by stabilization
around pH = 6.
pH
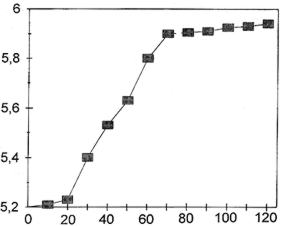
Time (hours)
Figure 6. Changes in the pH of the sodium citrate solution during pre-treatment.
Following this operation,
the engine was removed from the tank and rinsed with tap water under strong
pressure. It was noted at this time that the concretions had largely disappeared.
Further mechanical cleaning was performed to eliminate the magnesium-based
agglomerates. On conclusion of this step, some concretions were still
present on the iron alloy parts; we attempted to eliminate them by cathodic
polarization.
Cleaning of the ferrous parts under cathodic polarization.
The tank, still cathodically protected, was refilled, this time with 0.04M
sodium metasilicate (Na2SiO3). Cathodic polarization of the ferrous parts
of the engine requires electrical contact with all these areas. The aluminum
alloy parts are polarized only indirectly (by contact with the ferrous
parts); since they are very sensitive to the cathodic corrosion phenomena
[7, 8] induced by hydrogen bubbles formed on the surface of the metal
parts during treatment, the solution was vigorously agitated in their
vicinity to eliminate these bubbles. This was done by wrapping the engine
with a flexible rubber hose, which was then pierced in several locations
in proximity to the aluminum alloys and connected to the discharge from
a closed-circuit pump. The engine was then ready for immersion in the
solution.
Table 3. Cathodic potentials of the various metal parts of the BMW
801 D2 engine during cathodic polarization
of the ferrous parts in a 0.04M Na2SiO3 solution
Designation |
Without
polarization (V/SSE) |
Under
polarization (V/SSE) |
bearing
shafts (steel)
front
rear |
-0.73
-0.8 |
-1.04
-1.4 |
Cylinders
(aluminum)
heads
caps |
-0.83
-0.81 |
-1.3
-1.22 |
A second stabilized power supply was used for cathodic polarization of
the engine. Table 3 indicates the operating conditions used for this phase
of treatment, which lasted approximately ten days, after which the engine
was removed for examination. It should be noted that the stabilized power
supply used (Sodilec 12V/30A) made it possible to obtain average potentials
compromised between -1 and -1.4 V/SSE on the steel parts, and values were
lower on those situated near the anode cage (slight hydrogen bubbling
visible).
While this step was not as long as our previous tests at the AWM [10],
the solution used caused no observable corrosion of the aluminum alloy
parts. The inhibitor concentration used here thus appears to be more appropriate.
Following this operation, the engine was once again cleaned with tap water
under strong pressure. It was found that all the concretions covering
the ferrous parts had been eliminated. Before continuing with the cleaning
process, the solution was neutralized prior to draining; this was done
by adding anhydrous citric acid (21.5 kg) to reduce the pH from 12.4 to
a value close to 6.
Dechlorination
of all metal parts
-Top
Despite the non-aggressive nature of the medium in which the Focke-Wulf
190 was submerged at the time of its discovery, chloride ions were nonetheless
present in the materials. To extract them, we cathodically polarized all
the metal parts of the engine, using the same device described in the
second step above. In view of the low concentrations of chloride ions
anticipated, this treatment was performed in a sodium citrate solution
prepared with demineralized water.
Chloride concentration (mg/l)
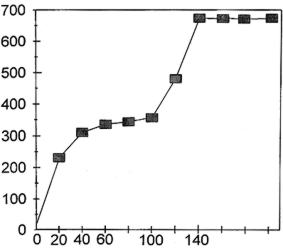
Time (hours)
Figure 7. Dechlorination curve obtained during cathodic
polarization of the entire engine in a sodium citrate solution.
The potential of the ferrous parts was maintained at -1.1 V/SSE, while
that of the aluminum alloy parts was closer to -1.5 V/SSE (average values)
because of their greater proximity to the anode. The pH of the solution
increased slightly (from pH 5.4 to 5.9), as in the preceding phase (see
Dissolution of surface corrosion products). After approximately
ten days of polarization, the engine was again removed from the tank.
This is the length of time normally used in many treatments of aluminum
alloy-based systems [7-10]; in addition, chloride assays performed using
the selective electrode on samples taken regularly throughout the polarization
process revealed that, by the end of this period, extraction had ceased
(Figure 7). It should be noted that these analyses must be performed immediately
after the samples are taken since the chloride ions are largely consumed
as a result of organic (bacterial) development in an unstirred sodium
citrate solution. We could have continued with additional dechlorination
phases to ensure total extraction of the chloride ions; however, by the
conclusion of this step we were already approaching our initial deadline.
Rinsing under cathodic protection and finishing
-Top
The engine was immersed in tap water one last time to eliminate all aggressive
species produced by the different electrolytes used in the treatments.
This brief (24h) phase took place under cathodic protection, with all
the metal parts of the engine connected to the cathode. The cathodic potentials
measured were slightly lower than those obtained in the preceding step.
We found no change in the pH of the solution. Following this rinsing,
a final mechanical cleaning was performed to remove the last corrosion
layers. The engine was then rotated on its horizontal axis to drain it
of any remaining water and dried with a stream of hot air.
The protective coating selected for long-term conservation of the engine
was the wax Dinitrol 4010, which is widely used by aeronautical companies
for storing engines prior to installation. This product, which consists
essentially of metal-organic compounds and polymers in a white spirit-type
solvent, is very similar to the Dinitrol AV 5B used in 1991 by the specialists
at the AWM to protect the Pratt & Whitney engine of the Hudson I A16-19
[10]. It is applied in spray form (average thickness per coat: 40µm);
it is transparent and has no effect on steel, aluminum, rubbers and plastics.
The engine was finally delivered to the Caen Memorial in September 1992.
Since that time, it has been displayed in a number of temporary exhibits
without showing any notable change in the various materials treated. At
the present time, it is in a storage box in the museums reserve
collection.
Discussion
-Top
The treatment of the BMW 801 D2 engine required only one month because
of its good general state of preservation. Additional dechlorination phases
would have been desirable, although on a composite item like this, it
is difficult to determine the stability of the materials involved; the
chloride ions extracted are derived, in fact, from both the steel and
the aluminum alloys.
In view of the success of this operation, the proposed procedure must
now be applied to other similar objects showing far more advanced corrosion.
For instance, in the case of the AWMs Hudson I A16-19 engine, which
was covered with very hard concretions over the iron alloys, we found
that three weeks of cathodic polarization in the Na2SiO3 solution were
barely sufficient to remove some of these concretions [10, 11]. It would
thus be interesting to study the behaviour of the indirectly polarized
aluminum alloys in this solution over a longer period. In addition, the
electrolytic parameters during the final cleaning in tap water under cathodic
protection are difficult to control because of the low conductivity of
the solution. Another electrolyte which is safe for all materials could
be considered [11].
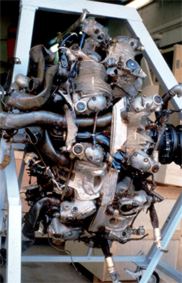
Figure 8. The BMW 801 D2 engine following treatment and protection
with the wax Dinitrol 4010.
The rubbers and plastics do not appear to have suffered as a result of
the various immersions. It might even be argued that their surface appearance
has improved (elimination of soiling and reduced opacity in the case of
the plastics). In fact, when this engine was exposed to the outside atmosphere
for one year following its removal from Le Loiret in 1990 and prior to
the beginning of treatment in 1992, these materials deteriorated as a
result of the effect of humidity, ultraviolet radiation and variations
in temperature. Since they could not be removed from the engine, we decided
to immerse and then protect them in the same way as the metal parts; regular
monitoring of their general characteristics during storage will enable
us to determine whether the solutions used are in fact harmful [11].
Conclusion
-Top
Treatment of a composite article is always difficult when the electrochemical
behaviour of the different materials is incompatible. The decision is
often made to separate these materials in order to stabilize them separately.
Here, we propose to treat the whole of a large object containing both
aluminum alloys and iron alloys, using chemical and electrolytic methods.
The proposed procedure involves four steps: pre-immersion in a chelating
solution to dissolve the surface corrosion products, electrolytic cleaning
of the iron alloys by cathodic polarization in a solution that inhibits
corrosion of the aluminum alloys, dechlorination of the entire object
by cathodic polarization and a final rinse under cathodic protection.
This treatment appears to have produced satisfactory results on a BMW
801 D2 engine from a FW 190 removed from Le Loiret River in 1990, but
requires further testing on other similar objects showing greater surface
corrosion.
Acknowledgments
-Top
I would like to thank Christopher Adams, a chemist at the Australian War
Memorial, and Carolyn MacLennan, a restorer, for their invaluable assistance
in the course of this project, as well as the Valectra Laboratory of Electricité
de France for allowing me to perform the work.
Suppliers
Sodium hydroxide: Prolabo, 12 rue Pelée, Paris, France.
Citric acid and sodium metasilicate: Lambert Rivière, 17 av. Louison
Bobet, Fontenay/Bois, France.
Expanded stainless steel (10 x 42 mesh, 1600 x 1000 mm sheets): EMT, 10-12
Bd des Martyrs de Chateaubriand, Argenteuil, France.
Electrical cable (2 x 6 mm2, ref RO2V): Société Franco-Belge
dElectricité, 61 rue du Lendit, Bt B. Aubervilliers, France.
Dinitrol 4010: Bonnot S.A., 183 rue Raymond Poincaré, Saulxures
sur Mosclotte, France.
Bibliography
1 GARREAU, G., Nungesser et Coli, premiers vainqueurs de lAtlantique.
Acropole (1990).
2 GILLESPIE, R.E., The Earhart project - an historical investigation,
TIGHAR 6 (1991).
3 HALLAM, D., and ADAMS, C., Finishes on aluminium - a conservation
perspective, in Saving the Twentieth Century: The Conservation of
Modern Materials. Ottawa (1993) 273-286.
4 LACOUDRE, N., Fana de lAviation 184 (1985) 11-12.
5 BOUSQUET, G., Les Dornier oubliés du lac de Biscarrosse,
Fana de lAviation 144 (1980) 43-47.
6 MacLEOD, I.D., Stabilization of corroded aluminium, Studies
in Conservation 28 (1983) 1-7.
7 DEGRIGNY, C., Mise au point dun traitement cathodique de
stabilisation de pièces en alliage daluminium dégradées
par corrosion en soution aqueuse, Ph.D. (Engineering) thesis, Paris
VI (1990).
8 DEGRIGNY, C., Conservation et stabilisation dalliages daluminium
prélevés sur des épaves aéronautiques immergées
en eau douce, in Conservation des Biens Culturels 3. ARAAFU (1991)
27-39.
9 DEBRIGNY, C., Mise au point dun traitement cathodique de
stabilisation de vestiges aéronautiques immergés en alliages
daluminium, in Saving the Twentieth Century: The Conservation
of Modern Materials. Ottawa (1993) 373-380.
10 DEGRIGNY, C., Traitements électrolytiques de vestiges
subaquatiques de grandes dimensions à base dalliages daluminium,
Archéologie en Yvelines 5 (1992) 30-49.
11 ADAMS, C., The treatment of the BMW 801 D2 radial aero engine
rescued from the Loiret river, RA 93 1034, EDF-GDL-Valectra (1993).
12 FLOWER, S., The Loch Ness Wellington in After the Battle
(1985) 42-47.Author
CHRISTIAN DEGRIGNY, born 1961. Engineer, Ecole Nationale Supérieure
dElectrochimie et dElectrométallurgie de Grenoble,
1985; Ph.D., Université de Paris VI, 1990; researcher, Valectra
Laboratory, Electricité de France, 1991 and 1992; assignment to
the Australian War Memorial in Canberra, 1991; currently with ART Métal
(O. Morel Lab), a laboratory specializing in the conservation of historic
metals.
Address: ART Métal (Labo O. Morel), 9 rue Mégevand, 25000
Besançon, France.
Back to site page
|
|